steel pipes Welding technology
Welding technology of steel pipes and profiles
Slab laser can not only enhance the quality, can progress to the competitive advantage.
In recent years, as people are increasingly concerned about environmental topics, in the progress of fuel efficiency, the pressure of car manufacturers are growing. More stringent, more binding regulations, the technical challenges to the industrial production and materials processing. These trends include lower emissions, the body lighter, as well as extend the life of the parts.
Advances in materials processing has brought a unique opportunity for the field of stainless steel production. Specifically, people asked the manufacturers to produce such parts, they must have a lighter weight, but still must have anti-corrosion characteristics and meet the strength requirements. In addition, the space limitations of the body exaggerate the importance of formability. Typical applications include exhaust pipes, fuel lines, fuel injectors and other components.
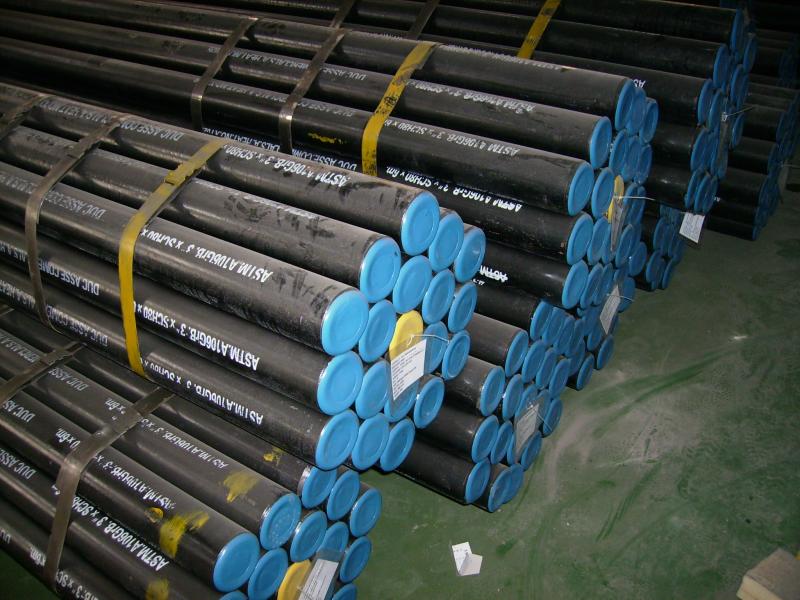
In the production of stainless steel pipe, the first forming the flat strip, and then makes its appearance to a round tube. Once formed, the pipe joints must be welded together. This weld seam greatly influence the formability of the parts. Therefore, to be able to meet the stringent testing requirements in the manufacturing of welding shape, select the appropriate welding technology is extremely important. There is no doubt that the tungsten inert gas shielded arc welding (GTAW), frequency (HF) welding, laser welding in the manufacture of stainless steel pipe to get the application.
Figure 1: The depth of laser welding with the intensity curve
Figure 2: different CO2 laser beam pattern
High frequency induction welding
HF contact welding and high frequency induction welding current equipment and provide the equipment of the extrusion pressure is independent of each other. In addition, both methods can use the bar magnet, it is a soft magnetic components are placed inside the tube, it helps to welding flow convergence in the strip edge.
In both cases, the strip is cut and clean up, roll up, and then sent to the welding point. In addition, the induction coil in the heating process for cooling the coolant. Finally, some coolant will be used in the extrusion process. Extrusion pulley role a great deal of force to avoid produce porosity in the weld zone; However, the use of a greater squeeze pressure will lead to glitches (or bead) increased. Therefore, a specially designed tool is used to remove the tube internal and external burrs.
One of the main upper hand of the high-frequency welding process, the steel pipe for high-speed processing. However, the typical situation in most of the solid phase weld, the high-frequency welding of the contacts using the traditional non-destructive technique (NDT) not easily conduct a reliable test. Welding cracks in the junction of the thin flat region at low intensity may appear, such cracks can not be detected using traditional methods, and thus may be the lack of reliability in high demand in automotive applications.
Tungsten inert gas shielded arc welding (GTAW)
Traditionally, the steel plant will Tungsten Inert gas shielded arc welding (GTAW) to complete the welding process. The GTAW between two non-consumable tungsten electrode to produce a welding arc. At the same time, the guide from the gun into the inert gas, in order to shield the electrode, resulting in the ionization of the plasma flow, as well as to protect the molten weld pool. This is an already established, and has been understood, it can be repeated to complete the high quality of the welding process.
The upper hand in this process is repeatability, welding process, no spills, and eliminates porosity. GTAW thought it was a process of electrical conduction, therefore, relatively speaking, the process is relatively slow. Figure 1 is a micrograph of the GTAW process typical metallographic structure.
High - frequency arc pulse
In recent years, GTAW welding power source, also known as high-speed switch, making the arc pulse to more than 10,000 Hz. Steel pipe factory's customers are the first to benefit from this new technology, high frequency arc pulse leads to arc downward pressure with conventional GTAW big five times. Brought about by the representative of the improved features include: the bursting strength is progress, and the welding line faster, waste reduction.
Customers of the steel pipe manufacturing plant soon discovered that the need to reduce the welding process, welding shape. In addition, the welding speed is relatively slow.
Laser welding
All pipe welding applications, the edge of the strip is melted, when using clamping bracket steel pipe edge squeezed together, the edge of coagulation. However, laser welding, the unique nature of it has a beam of high energy density. The laser beam melted the surface of the material, a key hole, as well as weld profile is very narrow.
The power density of less than 1 MW/cm2, such as GTAW technology, it does not produce enough energy density to produce the key hole. In this way, the process has been no key hole welding shape is wide and shallow. High-precision laser welding brought the penetration of more efficient, which in turn reduces the grain growth, lead to better metallurgical quality; the other hand, the GTAW higher the heat input into the slower the cooling process led to rough welded structures.
Generally speaking, people think that the laser welding process is faster than GTAW, they have the same rejection rate, while the former leads to better metallurgical properties, which brought a higher bursting strength and higher formability. When compared with the high-frequency welding, laser processing of materials, process of oxidation, which makes a lower rejection rate can be higher formability.
上一篇:Pipe standard terminology
下一篇:pipe technical requirements and methods manufacturing